The band of light on the forecourt of Brånebacken Museum in the Swedish town of Jönköping, comprising patterns that recall the history of the matchstick industry, draws visitors in and guides them towards the museum. The Swedish artist, Erik Vallbo, came up with the idea of a patterned band of light that, like an illuminated trail, recalls the town's matchstick history.
Traces in Motion, Jönköping/SWE
All fired up for a piece of remembrance culture
<p>This was anything but an everyday job for us. Realising the art project in the north-Swedish town of Jönköping called for our know-how as channel specialists, with our task being to develop and engineer the artistic covers which the adventurous industrial designer and artist, <a href="https://www.studiovallbo.com/">Erik Vallbo</a>, had designed for the project. Vallbo is known for his playful sound and light installations and nature-based objets d'art. In his Stockholm-based studiovallbo, the artist concerns himself with how technology and nature interact and creates unique nature experiences that constantly seek to arouse people's curiosity.</p><p> </p><p><strong>Playfully discovering the history of the location</strong></p><p>Vallbo pursued this very same goal when working on the art project in Jönköping. While doing research for the work of art to be installed on the forecourt of Brånebacken Museum, the artist had come across a collection of highly unusual graphically designed matchstick labels. Until some time into the 20th century, Jönköping had been a hub of Sweden's matchstick manufacturing industry and supplied all types of matches to all corners of the globe. This gave rise to the idea of arousing people's curiosity for the town's history through the creation of a dynamic sequence of these patterns. Incorporated into two bands of light, the idea was to have the shapes interact with each other and thus entice observers to work their way forwards and explore – "Traces in Motion" was born.</p><p> </p><p><strong>Creative team with a vast wealth of expertise</strong></p><p>As a bus route also cuts across the square, the bands of light had to be sturdy enough to withstand the heavy weight of a fully-occupied bus (load class D400). What initially looked like an unfortunate constraint actually put those involved on the right track: While considering how to combine a band of light with the variety of patterns and high load demands on the square that had been designated for the redesign, the subject of drainage also came into the equation. Although the drainage was not the primary concern, one thing quickly became apparent: In this field, specialists needed to be found who were capable of solving such technical problems. Through our distribution partner Ulefos, we were thus brought in to the international creative team.</p><p> </p><p><strong>Solution needed for an enormously heavy issue</strong></p><p>The task involved finding a production technology and solving the load issues that weighed heavily on the project. Two sample bands comprising a large number of assorted designs needed to run parallel to each other – this was the idea envisaged by<a href="https://www.studiovallbo.com/"> Erik Vallbo</a>. Given the very diverse nature of the patterned slabs, however, ductile iron was not found to be a suitable material for the production of the covers: The large number of moulds that would have been required would render it uneconomical and the result in less sharp-edged products. Corten steel ultimately became the option of choice. This material is weather-resistant and allows filigree patterns to be laser cut.</p><p> </p><p><strong>Filigree patterns in hard steel</strong></p><p>A large portion of the project involved exploring patterns and shapes that can withstand such a high degree of pressure. Erik Vallbo had prepared over 30 patterns, 17 of which were ultimately implemented.</p>
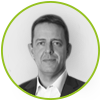
We needed to examine whether the patterns could even be lasered from the corten steel plates; at times, all that was missing was a certain radius. And, on the other hand, the ability to drive over the patterns also needed to be guaranteed. Tests and calculations were run to establish this,
<p>recalls our Product Manager, Ulrich Groth. Multiple load tests later, twenty-millimetre corten steel proved to be the thickness best suited to absorbing the loads. The cover is placed over our BG-FILCOTEN NW 150 pro G standard channel. Made of sustainable, high-performance concrete, the channel body combines high stability with minimal environmental impact. The flexible channel system can withstand loads up to class E 600 (in accordance with EN 1433). In the end, two forty-metre long channel runs were produced for the museum's forecourt, both running parallel to one another and separated by two rows of steel pavement slabs. LED strips were inserted into the channels to backlight the patterned bands. </p><p> </p><p><strong>Creative production for the future</strong></p><p>"Unusual projects like this one really only ever come around once in a blue moon," recalls Ulrich Groth while reflecting on the successful collaborative efforts of the small-scale team.</p>
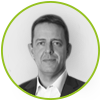
Collectively overcoming these challenges, sounding out the various possibilities: that was a lot of fun. The corten steel manufacturing method that we developed here will make it much easier to offer similar work jobs in the future.
Project profile
Project name
Traces in Motion
Location
Jönköping, Sweden
Installed channel types
BG-FILCOTEN® G NW 150
Grating types:
Corten steel designer grates
Total length in metres
80 m
BG-Project team:
Ulrich Groth, Wolfgang Strandl, Christoph Lettner
Architect/planner
Partners:
Ulefos AB, Stenkullen, Sweden
Mr. Peder Svensson