Successful premiere from the get-go: This was the first time that BG-Graspointner had taken on the full site supervision role for a drainage system.
Every challenge welcomed
Parking areas at the Institute of Science and Technology
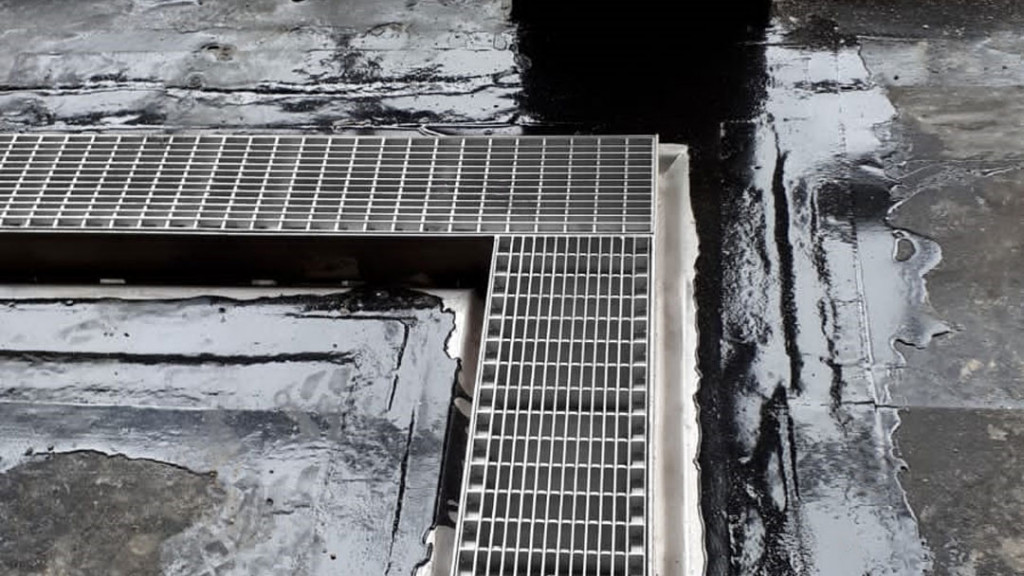
As it is slightly water-permeable, a layer of bitumen was applied first that also directs small amounts of water into the channel.
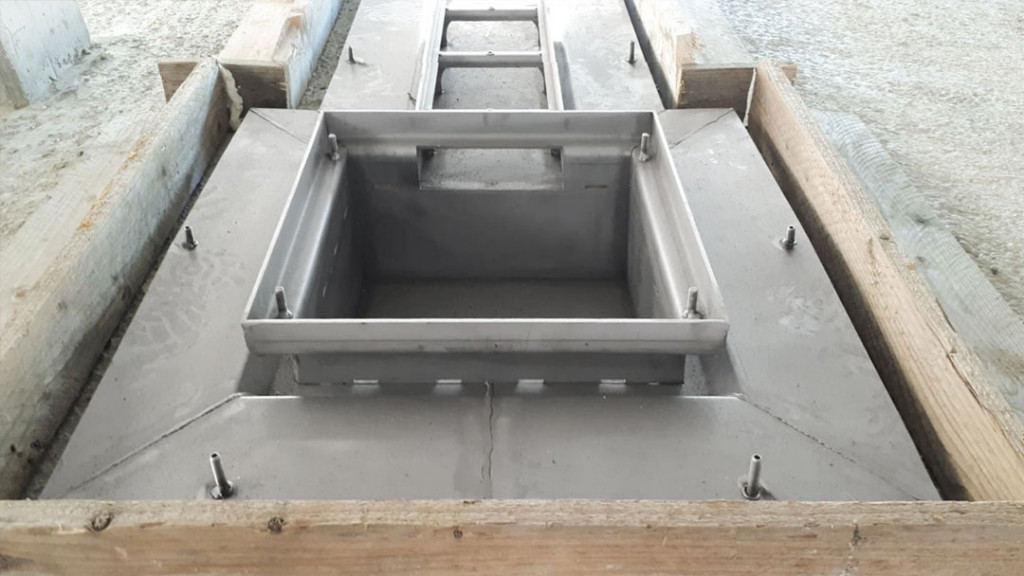
The channel body comprises two drainage levels. Both had been welded together in the plant into 1-metre lengths prior to installation.
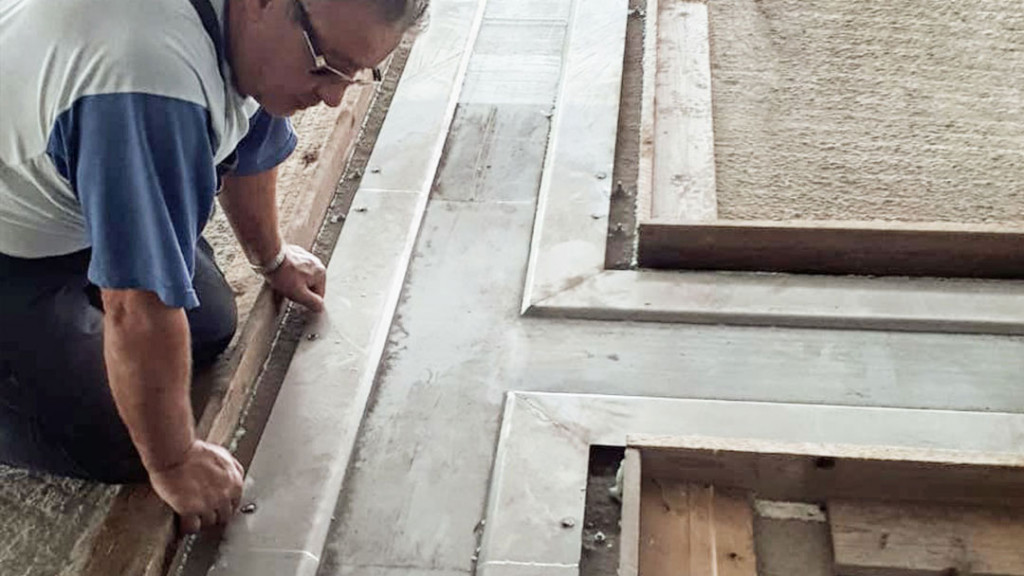
The feet were specifically designed for this project in response to the varying construction heights inside the building. Lasers were used to ensure they were perfectly aligned down to the last millimetre.
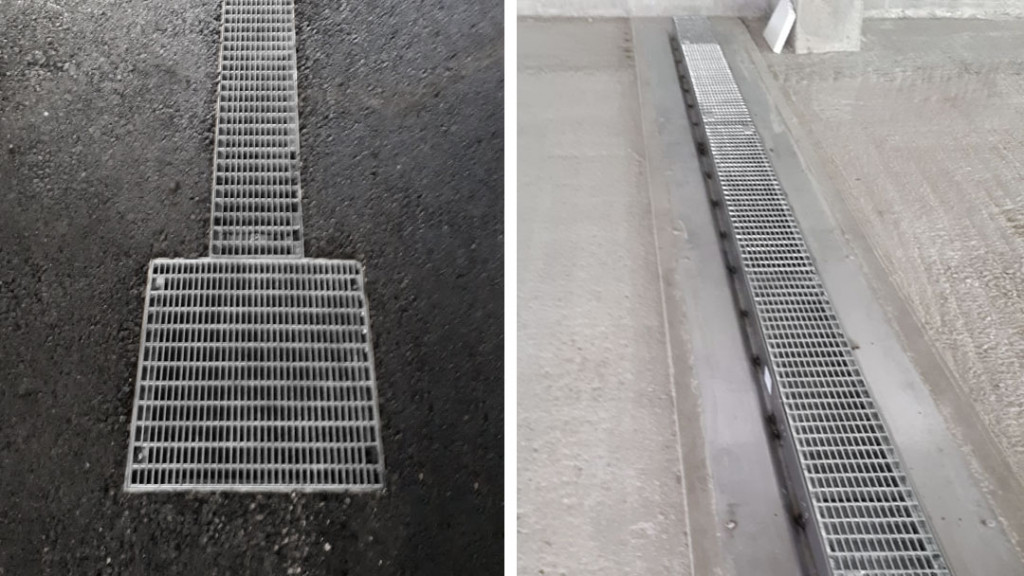
The client was also pleased with the result: "BG-Graspointner is one of our partners of choice for upcoming projects."

Successful premiere from the get-go: This was the first time that BG-Graspointner had taken on the full site supervision role for a drainage system.
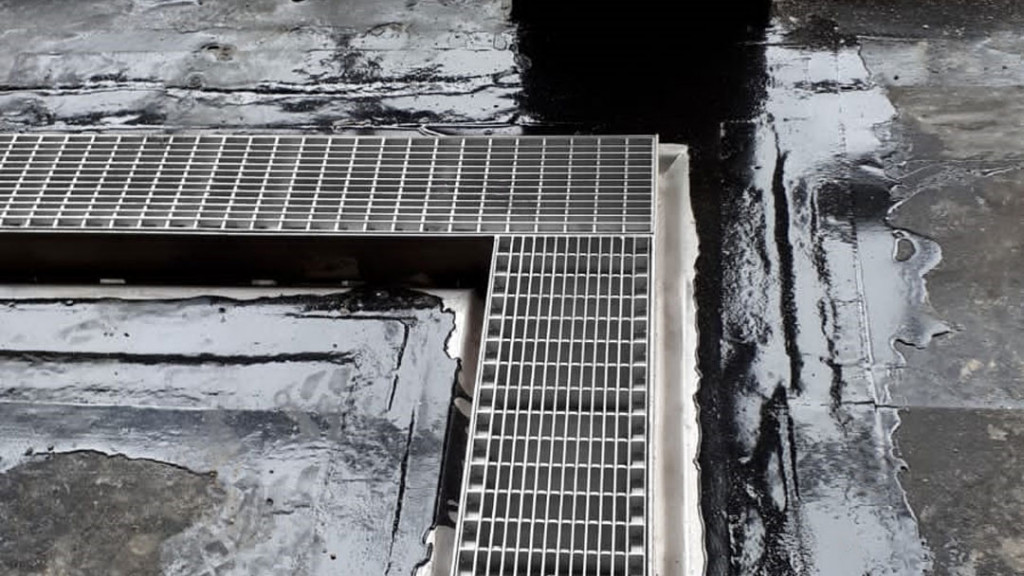
As it is slightly water-permeable, a layer of bitumen was applied first that also directs small amounts of water into the channel.
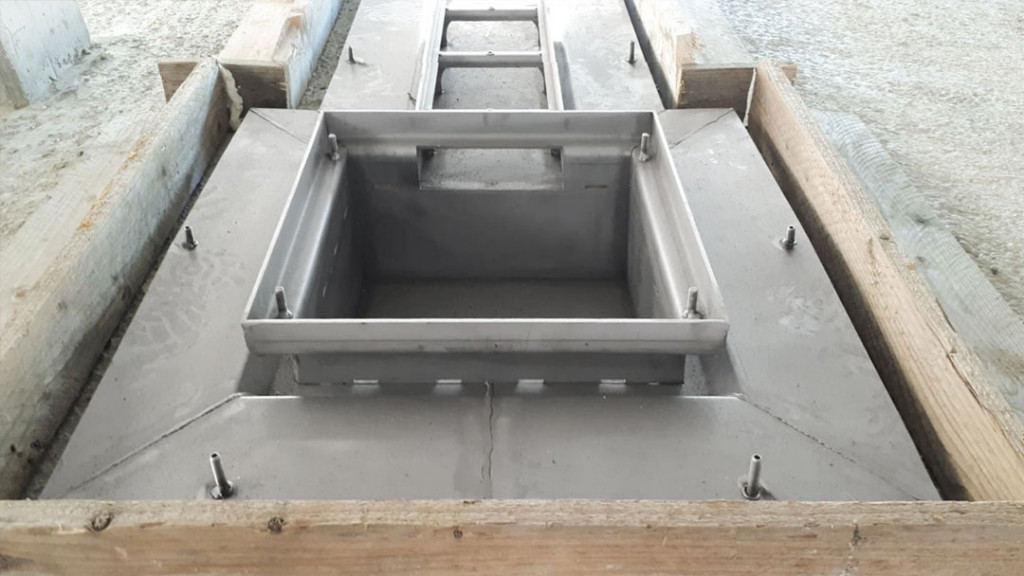
The channel body comprises two drainage levels. Both had been welded together in the plant into 1-metre lengths prior to installation.
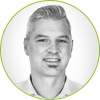
From the very outset, we were aware of two things: First: With this project, we were entering new ground. Second: We are up to the task.
Whether the many custom-built products or the final acceptance, this was a demanding project on all levels, but their solution-oriented approach and the quality of the delivered results make BG-Graspointner one of our partners of choice for future projects.
Project profile
Project name
IST Maria Gugging
Location
Maria Gugging, Austria
Installed channel types
BG-FLEX V2a stainless steel evaporation channels with a second drainage level, sealing flange and adjustable feet included.
Grating type:
BG-FLEX FA mesh grating NW150 V2A, MW30/10, cl. C 250kN, locking bolts included.
Total length in metres
478 m
Services BG-Support
The product specifications requested by the architect and the client were perfectly implemented by our team of technicians!
- The channel body load class C 250kN was accomplished.
- Varying V2a stainless steel channel body heights
- Extra-wide sealing flange for the bitumen seal
- Plan drawing and marking of the individual channel bodies and/or custom parts
- Creation of a bill of materials for the installation company
- Handover to the installation company
- Assistance with the monitoring of the installation work
- Final inspection involving the construction and installation companies
- Adherence to deadlines, even during the difficult Covid-19 era
Client/owner
BG project team members
Robert Eder, Christoph Soriat, Dominik Stockhammer, Josef-Mario Resel
Architect/planner
Maurer u. Partner, Arch. Georg Siegel
Building contractor
Bauleiter Swietelsky Dipl. Ing. (FH) Gerald Berndl, M. Eng.
MMG Mühringer Montage GMBH
Robert Eder
Technical Support
BG-Graspointner | Austria
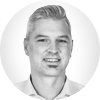